Home > Plastic Auxiliary Equipment > Plastic Regrind and Washing Systems |
Plastic Regrind and Washing Systems |
As plastic is a not biodegradable so it is important that all the waste product that comes out of plastic molding industry/process be recycled. In addition to being beneficial for the environment we live in, this practice also makes the plastic molding process cost effective as the waste material are recycled and used to make new molds. Plastic Regrind and Washing System involves a few processes to upgrade virtually any rigid post-consumer or post-industrial plastic, so that it can be used again to manufacture new molds.
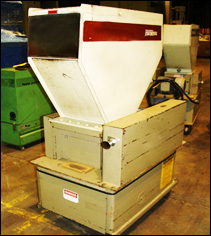
Processes Involved:
The entire process of plastic regrind and washing involves the following stages:
- Washing
- Rinse
- De-watering
- Drying.
Washing: In this stage, the waste material is thoroughly washed by continually submerging, spraying, and flushing with a heated closed loop wash solution. The concept behind the use of heated water is that the combination of the heated water and attrition scrubbing from particle to particle contact provides exceptional cleaning which is not possible with normal water. The dissolved contaminants and small particles are sieved out and removed.
Rinsing: This stage employs a spray clean heated water (appox. 180F) to rinse away the remaining wash solution and prepare the cleaned material for tumble de-watering and drying.
De-watering: This process is executed mainly to agitate and remove the remaining moisture from the plastic materials. The water is collected in the common wash/rinse sump so that i can be continually revitalized.
Drying: This is the last stage of the process and demands a lot of precision and expertise. Generally this phase is performed by one of the following two methods two methods:
Rotary Drying: Rotary drying is done by subjecting the so prepared materials to a gush of hot air at abut 60 mile per hour. These rotatory dryers can be made and integral part of the washing/rinsing unit or can be a separate individual unit depending on specific requirements and convenience and it can be electrically configured or by gas.
Centrifugal Drying: This is the second method of drying, which involves a different unit. It utilizes high rotational velocities to take away the moisture. The optional counter-flow hot air can be used to ensure additional drying.
|
|
|
 |