Home > Material > Occasionally Used Materials > Silicone |
ABS(Acrylonitrile butadiene styrene) |
Possessing the toughness of polybutadiene rubber, ABS or Acrylonitrile Butadiene Styrene has good conjunctive strength. Derived from Acrylonitrile, Butadiene, Carbon, and Styrene, ABS has the rigidity of Acrylonitrile & styrene polymers. It is an occasionally used material of rotational moulding process.
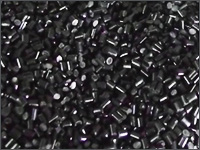
The most important fact of ABS are its durability and toughness. Various types of modifications and transformation can be done to improve the quality and level. The impact resistance can be initialized by increasing the level of polybutadiene in relation to styrene and also Acrylonitrile. The properties of ABS compositions can be altered for its use in different applications like extrusion, injection moulding etc. Changing of ABS composition can provide the property of high or medium impact resistance. Generally, ABS would have useful characteristics within a temperature range from 10 to 80 °C (50 to 176°F). In rotational moulding process ABS play a essential role to provide the high end quality work output.
The final output will be affected to some extent by the conditions and procedures under which the component is processed to the final product . For example, molding at a high temperature improves the gloss and heat resistance of the product whereas in rotational moulding process molding in a low temperature improves the rigidity and toughness of the product.
ABS in rotational moulding is long and continuously growing material, that was initially used infrequently. Its top features are easy to mould and light in weight. It assists in manufacturing products, some of which are listed below:
- Drain-waste-vent (DWV) pipe systems
- Golf club heads (due to its good shock absorbence)
- Luggage and protective carrying cases
- Musical instruments
- Small kitchen appliances
- Toys for children
The ABS plastic, which is grounded to an average diameter of <1 micrometer finds usage as the colorant in few tattoo inks, making them distinct in nature. This is the most obvious indicator that the ink contains ABS, as tattoo inks rarely list their ingredients. ABS is the special ans essential component in rotational moulding process. Due to its easy moulding feature it can be transform and moulded into any sought of attractive designs and structure.
While the cost of producing ABS for the process of rotational moulding it is roughly twice the cost of producing polystyrene, ABS is considered one of the best component for its hardness, gloss, toughness, and electrical insulation properties. ABS is flammable when it is exposed to high temperatures, such as a wood fire. It will melt, boil, then burst extensively into extreme hot flames.
|
|
|
 |