Home > Different Industrial Molding Processes > Thermoforming |
Thermoforming Process |
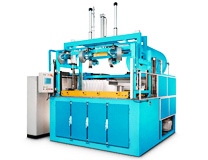
What is Thermoforming?
Thermoforming is a relatively simple and inexpensive manufacturing process that involves heating of plastic sheets and and transforming them into specific usable shapes. Although this process of molding was mainly used for producing food packing materials such as blister papers and disposable coffee cups, the cost andtime advantage associated with this process gradually led to its usage in a broad spectrum of industrial products. Presently thermoforming is employed in a wide range of applications from plastic toys, cafeteria trays to aircraft windscreens. Thin-gauge (less than 0.060 inches) sheets are mostly used for rigid or disposable packaging, while thick-gauge (greater than 0.120 inches) sheets are typically used for cosmetic permanent surfaces on automobiles, shower enclosures, and electronic equipment. There are different types of thermoforming process like plastic thermoforming, rotary thermoforming, rubber thermoforming, rotational thermoforming, plastics & rubber thermoforming, etc. But the most popular one is plastic thermoforming.
Understanding Thermoforming Process:
The process of thermoforming involves the following steps -
- Extrusion of sheet
- Placing the sheet on mold
- Drawing sheet into the shape of the mold through heat & negative force (vacuum)
The machines used in the process are called thermoforming machinery. Manufacturers, suppliers and exporters based in India adhere to the industry guidelines while fabricating thermoforming machines.
Types of Thermoforming Process:
Vacuum Forming – In this process a vacuum is formed between the mold cavity and the thermoplastic sheet. The pressure produced by this vacuum, which is about 14 to 16 psi, conforms the sheet to the mold and shapes the part.
Pressure Forming – Pressure forming employs an additional air pressure, of about 50-100 psi, on the back side of the sheet to help force it onto the mold. This air pressure allows the forming of thicker sheets and produces finer details, textures, undercuts, and sharp corners.
Mechanical Forming – Mechanical forming is quite a simple process. Here, mechanical force is directly applied to the plastic sheet, which is forced into or around the mold. A core plug pushes the thermoplastic sheet into the cavity of the mold force it into the desired shape.
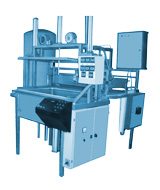
Materials Used in Thermoforming Process:
- Acrylic (PMMA)
- Cellulose Acetate
- Acrylonitrile Butadiene Styrene (ABS)
- High Density Polyethylene (HDPE)
- Polystyrene (PS)
- Polypropylene (PP)
- Polyvinyl Chloride (PVC)
Contact us for the details of manufacturers, suppliers and exporters of thermoforming machines, plastic thermoforming machines, rotary thermoforming machines, rubber thermoforming machines, rotational thermoforming machines, plastics & rubber thermoforming machines in India. You can send your any query regarding thermoforming process or any thermoforming machines.
|
|
|
 |